
FLEET SERVICES
McCormick believes that the maintenance of equipment and vehicles represents a vital role in service delivery in every patient encounter. For that reason we service each vehicle through an aggressive Preventive Maintenance (PM) schedule and track all maintenance services with extensive documentation.
Our PM program anticipates parts replacement in advance of potential vehicle failures and provides servicing exceeding manufacturer recommendations. The Maintenance Department uses only manufacturer recommended lubricants, fluids and service parts, therefore conforming to Ford’s specifications as provided by the dealer.
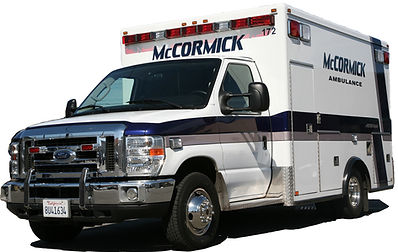
The company’s driver-operators participate in our preventive maintenance program by performing a daily pre-trip inspection of the ambulance. This helps identify problems in their formative stage, and safety-related defects are repaired promptly. Most of the maintenance work performed, approximately 98%, is Scheduled Maintenance: preventive maintenance inspection, driver-operator documentation, and planned component repairs.
McCormick’s insistence on a safe, modern and healthy work environment assists the company in attracting and retaining a skilled and motivated team of maintenance specialists.
Our maintenance technicians average more than 20 years experience in emergency vehicle repair and bring a wealth of diesel ambulance preventive experience to the company. They have a vast knowledge of technology developments for diesel powered engines as well as specialized knowledge of emergency vehicle maintenance; this is achieved through training and through working exclusively on one type engine. All of our ambulances are Ford diesel or gasoline powered engines.
Every 5,000 miles, the fleet maintenance team performs a systematic bumper-to-bumper inspection, examining more than 145 components, followed by comprehensive service averaging 3.5 hours per vehicle. The technicians inspect all major components, including engines, transmissions, cooling, and electrical systems, replacing them as needed.
The Maintenance Department uses a computerized system to schedule and track maintenance for every vehicle. Each vehicle has a maintenance history file containing everything from oil changes to any repair performed. Meticulous record keeping enables the maintenance team to remain consistently efficient, thorough and precise, and document performance for quality improvements. The department monitors and logs vehicle mileage on a weekly basis to ensure that preventive maintenance inspections are scheduled every 5,000 miles.
In-house maintenance gives us the opportunity to manage our own resources more efficiently, i.e. man-power, parts, facility, scheduled and unscheduled activities. Scheduled activity is more efficient, by regularly setting time to diagnose and repair, if necessary; replacement parts are stocked “in-house”, minimizing vehicle down time. Our shop can balance vehicle repair for peak activity control. This allows shop staff to meet all of the fleet needs.
In-house maintenance also gives us the opportunity to measure, monitor and provide feedback, which is essential to a great emergency vehicles maintenance program. This allows identifying problem areas, which can be studied and corrected. On a weekly basis we have a Key Performance Indicator Report for our maintenance department, which identifies any potential problems in this field, as a beneficial tool.
McCormick management supports and requires our crews to inspect their assigned unit and equipment, complete the daily check-out form, and report any noted malfunctions immediately. Communication is an extremely important step to reduce vehicle break down and to achieve the best possible results.
The maintenance department supports our organization by providing reliable and safe units for our operations, by responding quickly to every demand, keeping records for our maintenance activity, and is on call 24/7.
All of the above ensures safety, and minimizes disruptions of service for our patients, crews, and the general public.